One of the most important pieces to the puzzle when installing modern day windows is how to manage water. Any new window is expected to seal out wind and water from between the sash and the frame, but how does one ensure keeping water out of the rest of the rough opening? Let’s talk about a few key elements in using the most up-to-date and effective types of flashing; adhesive-backed flashing tape.
Read the Full Article
There are several types of flashing tapes available, with the majority being produced with three types of adhesive: asphalt, butyl or acrylic, as well as some hybrids. Most window manufactures recommend the use of butyl-base or acrylic-based adhesives. Almost all window manufacturers recommend not using asphalt based adhesive. The chemicals in asphalt adhesives can cause window flanges to deteriorate over time. Always follow the Manufactures recommendation when choosing the flashing tape.
Taking the proper time to install a window can seem labor-intense and expensive, but a necessity to keep moisture out. This added time and expense if far less than the cost of call backs when water is found leaking in through an improperly installed or flashed window.
Installing the Window – Let’s assume the building paper has been properly cut back to expose the window opening. Prior to putting the window unit into a rough opening, steps need to be addressed to make sure sills are flat and level and a sill pan is covering the base of the RO and turned up the sides. The next step is to place a bead of sealant to the jambs and head of the window opening making sure not to put sealant on the sill (meant to allow moisture to escape out through the sill opening). Place the window into the opening, check for plumb and level and install fasteners to Manufactures specifications.
Once ready for flashing, the first step with the tape is to line up one side of the exterior frame, and cut the tape to length to roughly the width of the tape (usually 3”-6”) longer on the bottom and at the header. So, if you have 4” flashing tape, cut your jamb piece about 6”-8” longer to go past the head and sill. Another very important step is to make sure the tape is fully covering the nail flange, rolling the tape up onto the edge of the frame about ¼”. The tape should extend out over the nail flange and onto the weather barrier. Follow the same instruction for the opposite jamb.
Installing the flashing tape to the head or top of the window:
The flashing tape should extend past the jamb flashing tape by approximately 1”. Ensure the flashing tape adheres to the edge of the window by a ¼” and extends over the nail flange and onto the sheathing. Now that all three sections have been installed, use a wheeled roller to press the flashing tapes securely onto the nail flange and weather barrier. Bring the top weather barrier down over the head flashing tape and secure the seams with tape.
This is a brief explanation of a basic window flashing detail. Following Building Code and the Manufactures recommended practices is of the utmost importance. A properly flashed window should keep water from entering and allow moisture to escape the rough opening through the sill.
According to the Associated General Contractors of America, 70% of construction companies are having trouble finding qualified workers. “Over the last four years, we’ve seen rising rates of open jobs,” said Robert Dietz, chief economist for the National Association of Homebuilders.
Read the Full Article
During the Great Recession that began in 2008, more than 1.5 million residential construction workers left the industry. Some changed careers; others simply retired. Many immigrant workers went home and never came back. Today, 10 years later, the industry has recovered fewer than half of those jobs. And by one estimate, for every skilled worker entering the workforce, there are five who retire.
“If we don’t get workers, housing costs are ultimately going to be even higher,” Dietz said, “and that’s going to price out workers from being able to own their own homes.”
We can’t blame it all on the recession, though. In a recent report, the Washington State Auditor found that good jobs in the skilled trades are going begging because students are being almost universally steered to bachelor’s degrees.
“There is an emphasis on the four-year university track,” said Chris Cortines, who co-authored the report. It’s an entrenched belief – promulgated by universities, guidance counselors, parents, peers and the media – that without that four-year university degree a child will have no future. Yet according to the National Student Clearinghouse, 30% of high school grads who go to tour-year public universities do not earn a degree within six years of enrolling. Obviously, college is not right for everyone. Sadly, there are still negative perceptions that “Vo-Tec” is for kids who are dumb, poor or lazy. It’s tough enough to be an adolescent these days without those labels being hung around one’s neck. It’s easier to jump on the college-bound bandwagon. What can be done to get more workers? Here are three ideas:
Early Awareness. The Washington State Auditor recently recommended that career guidance – including choices that require less than four years in college – start as soon as the seventh grade (even earlier, in our opinion). Schools and especially parents will need to buy into this, but if we can just let kids know they have choices, and that they’ll be supported in those choices, it will make the high school experience a lot less stressful (and possibly safer) for everyone involved.
Marketing. We need to make the trades “sexy”; dump the stereotype of the overweight plumber with a butt-crack problem and present skill laborers as role models. The next time you see a TV ad recruiting for our armed forces, listen to what they are saying to make the military appealing to young people: you’ll have an adventure; you’ll learn a marketable skill; you’ll use technology; you’ll work side-by-side with some really great people. We need to promote the trades in the same way. Building a house should be cool!
Financing. Tennessee has made its technical colleges free. We think NH should do the same
Agree? Disagree? Have other ideas to encourage young people to enter the trades? Send to Dan@Selectwood.com so we can continue this conversation.
Last year, after a one year “cooling off” period, the United States Chamber of Commerce imposed a countervailing/anti-dumping (CVD/AD) duty of approximately 24% on all Canadian softwoods imported into the country.
Read the Full Article
The basis of the U.S. Canada trade dispute, which began in 1982, is a claim that Canada’s lumber industry is unfairly subsidized through reduced stumpage fees (the price paid to the landowner to harvest timber), as the federal and provincial governments own the lion’s share of the timber land and set their fees administratively rather than through the competitive marketplace. In 2006 the United States and Canada agreed to a resolution to end the dispute. This resolution was titled The Softwood Lumber Agreement and by the end of the year was fully in place. The agreement held somewhat fast with several changes and an extension until the end of 2015. The moratorium on the trade actions “cooling off period” was in place until October of 2016 when talks about new CVD/AD began becoming official at the end of April 2017.
There are several points to consider when discussing/debating the countervailing and anti-dumping duty action. The United States is Canada’s largest market for lumber, as domestic producers do not have the capacity to produce enough of the materials needed. Based on information gathered by the National Lumber and Building Material Dealers Association and the Northeastern Retail Lumberman’s Association, most of the northern states and specifically the northeast use SPF framing lumber NOT produced in the U.S. Softwood lumber accounts for 10.3% of the overall cost of housing. The instability resulting from not having a Trade Agreement and the exorbitant duties is causing drastically increased prices for new homes. There is also one aspect of the tariffs that has not been discussed and which impacts Selectwood’s business specifically; nearly all Western Red Cedar and Douglas Fir uppers along with Western Hemlock is sourced though Canada and cannot be provided by U.S. lumber suppliers.
Lastly, on March 15th, 2018, U.S. Customs and Border Protection (CBP) determined that coniferous shingles and sawn shakes from Canada fall within the scope of the CVD/AD cases and must be included with payment of duties. This includes all Western Red Cedar, Alaska Yellow Cedar and Easter White Cedar shakes and shingles. This new interpretation of the 36-year-old dispute immediately added a 21% duty to these products.
While our lumber and building materials industry overall is certainly aware of the importance to keep a fair trade balance with all of the countries we partner with, it is equally important to recognize that products which are unavailable in the United States should not be subject to these exceptionally high duties and tariffs, or perhaps any tariffs at all. And one question that is often asked is, “Where do the dollars collected from the CVD/AD tariffs on Canadian softwoods ultimately end up going?” Inquiring minds want to know.
When Selectwood’s co-founder and co-owner, Peter Robart died last May after a long battle with cancer, it left huge holes – not only in the hearts of those who knew him, but in communities all around the Seacoast, as well as throughout our industry…from here in New England, all the way to British Columbia. If you were to ask people, “What’s the first word that comes to mind when I say Peter Robart?” you would hear words such as “Kind”…”Generous”…Energetic”…:Fearless”…”Honest”…Optimistic.”
“One of the main reasons Selectwood
became so successful is that Peter made
some very shrewd investments…in people!”
Read the Full Article
These are the traits people most readily associate with Peter. And while every single one of those words is accurate, underneath that outer layer of happy warmth and positive energy beat the heart of a very smart businessman – one who for more than 30 years helped to grow and shape the retail lumber industry in northern New England. Selectwood came into existence because of Great Bay Spa & Sauna, the hot tub business started by Peter and his partners, Mark Rudd and Dave Wason. One day, one of their customers who had purchased a Redwood hot tub from them, had a complaint. The tub was so beautiful, he said, it made his pressure-treated deck look cheap by comparison, and was there any way he could order some Redwood lumber to replace his deck and match the tub? A light bulb went off. A container of Redwood was shipped from California to NH. Selectwood was born.
From that humble beginning, Peter and his partners grew Selectwood into one of the premier lumber retailers in New England. Selectwood was the first retail company in North America to join the Western Red Cedar Lumber Association, and it has been an active participant in the New Hampshire Retail Lumber Association, the Cedar Shake and Shingle Bureau, the American Institute of Architects and several other industry organizations.
One of the main reasons Selectwood became so successful is that Peter made some very shrewd investments…in people! Did you know Peter majored in Psychology at UNH? Given his success and his predilection for politics, many people would assume Peter majored in Business or Political Science, but no, he studied human behavior. Several years ago, on a golf trip to Florida, Peter said to one of his playing partners, “Anybody can buy at wholesale and sell at retail. To be truly successful, you need to create positive interaction between the people you are buying and those who are selling. You have to build a relationship built on mutual respect and trust.”
To ensure that this happened at Selectwood and Great Bay Spa & Sauna, Peter made it a point to hire very good people and treat them with total respect so that they knew they were valued. Inspired by Peter’s example, the people he hired treated customers and suppliers with respect so that they knew they were valued. As a true believer in the phrase, “A rising tide lifts all boats,” Peter went out of his way trying to turn first-time customers into regulars, and suppliers into partners. And he did it all with grace, humor and integrity.
Over the years, under Peter’s leadership, Selectwood and Great Bay Spa & Sauna received several awards and accolades from their respective peers. Yet Peter would be the first to tell you that these moments of recognition, however gratifying, are not what constitute a legacy. It doesn’t matter how many brass plaques hang on your wall, or glass trophies sit on your credenza – they will all eventually be put in a box and forgotten. What is never forgotten, though, is how you treat others. And that is the true legacy of our friend Peter Robart.
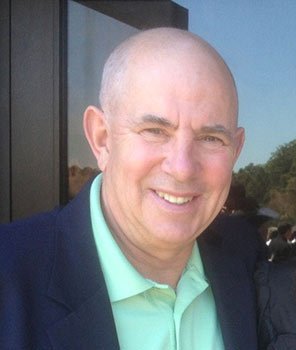
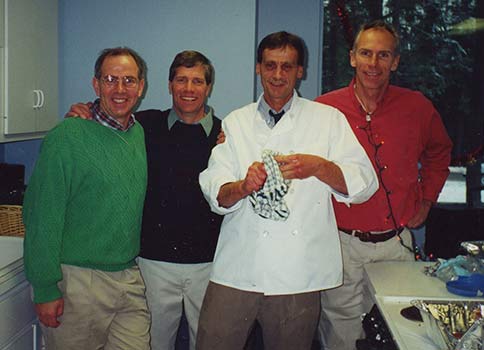
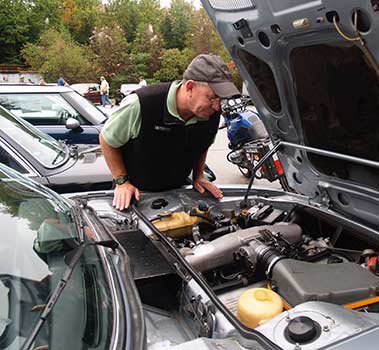
Marvin at 7 Tide is a one-of-a-kind design destination located in South Boston’s Innovation District. The high-tech, high-touch facility opened its doors in July of 2016, inviting homeowners, architects, design professionals and Marvin retail locations like Selectwood to explore, discover, design, and collaborate.
Read the Full Article
EXPLORE – Marvin at 7 Tide illustrates the exceptional craftsmanship and rich history of Marvin Windows and Doors. We invite you to take a peek inside and see what makes Marvin so special. More than just wood, metal, and glass, windows and doors provide light, define spaces, frame views, and connect the indoors and out.
DISCOVER – Find your unique style. Browse the inspiration gallery to pinpoint exactly what you’re looking for. From traditional to contemporary, and everywhere in between, Marvin at 7 Tide throws open the windows and doors to a myriad of possibilities.
DESIGN – Marvin at 7 Tide supports your design vision with hands-on technology resources, bringing Marvin windows and doors to life. Roll up your sleeves and experiment with scale, wood species, finishes, and accessories. If you’re on the fence between shooting for the stars and playing it safe, we know you’ll leave feeling confident in your final selection.
COLLABORATE – Marvin at 7 Tide allows you to fully visualize your window and door needs, leaving nothing to get lost in translation. It provides a great place to meet up with your Selectwood representative, architect, contractor or interior designer to hash out the details of your project.
Marvin at 7 Tide is open for walk-ins and by appointment Monday through Friday 10 am to 6 pm and Saturday 10 am to 4 pm. Visit www.seventide.com to learn more.
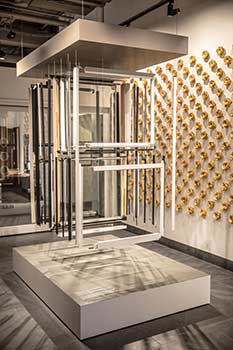
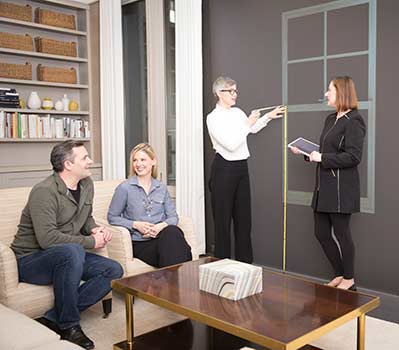
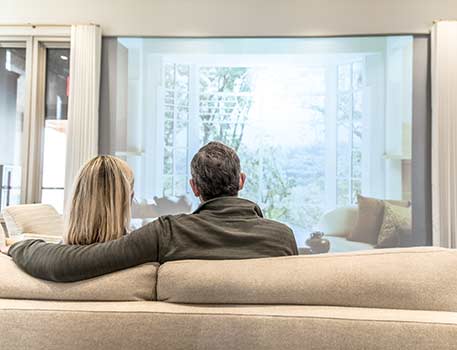
A Contractor’s Tale
Not too long ago, a contractor pulled into Selectwood in a brand new, full-size pickup with enough payload, torque and horsepower to haul the Statue of Liberty up Mt. Washington. We teasingly remarked, “You think that truck’s big enough?” He defended his purchase by rattling off a laundry list of all the demands his truck had to meet – it needed this much towing strength, this much load capacity, this size bed, room for this many crew members, this many air bags, brakes that were this big, this long a warranty, etc. He concluded by saying that although it was expensive, it would save him so much time, money and headaches compared to his old truck, he’d make it back in no time.
Read the Full Article
It was then we noticed that a number of tools sitting in the bed of his truck were the brands you’d find in a Big Box store. We asked him if, when buying tools, he used the same logic he used to make his truck-buying decision. No, he said. For him, the tools were so inexpensive it was as if they were disposable. “I use one until it fails, then buy a new one.” What about Festool, we asked? “Way too expensive. I can’t justify it.” So we loaned him our personal Festool TrackSaw (portable circular saw with guide rail) and told him to try it for a while.
He came back within a few days and bought his own, plus a few other Festool products.
The moral of the story? Just because a truck or a tool is expensive doesn’t mean it’s not worth every penny. Yes, Festool products cost more, but they save you so much in time, materials and health benefits, they pay for themselves in short order.
“Of course you folks would say that,” you’re thinking. “You sell the stuff.” Yes, we do – because we truly believe in it. And don’t just take our word for it – check out what a couple Festool fanatics have to say:
Bradlee Kirkpatrick, OCHO Woodworking & Design, Portsmouth, NH.
“I’ve been using Festool products for a very long time. I own a Track Saw 65, which is so old they no longer make it – it’s been replaced by two other models – and it just keep going. I also have a 15-volt portable drill that has suffered incredible abuse and still performs great. My favorite is the Rotex 125 [multi-mode sander] that I connect to a Festool dust vacuum. I just used that combination to spiff up the bottom of a 32-foot lobster boat in no time… upside down, and no dust in my face!”
Andrew Neubauer, Neubauer Carriage Doors, Dover, NH
“I first started using Festool about 4 or 5 years ago. I’d known about the line for a while but just couldn’t get past the cost. How could a tool be that much better than the DeWalt or Rigid I was using? Then a friend loaned me his Festool sander and dust vacuum system. After using it for just a couple of days, I bought my own. I work almost exclusively with cedar and mahogany, both of which produce some pretty noxious dust. I couldn’t believe how much the Festool system reduced the dust I was being exposed to. Now I hardly ever wear glasses or a mask, and cleanup is super quick. Based on that experience, I went out and bought a bunch more Festool products – both the large and small TrackSaws, the Kapex sliding compound miter saw, a router, and the Domino joiner. I can’t say enough good things about Festool.”
About Festool
Festool is a complete supplier for all applications involving wood. Whether sawing, routing, sanding, planing or extracting dust, Festool has the ideal power tool for every application. Festool tools and accessories are designed to work together in a completely integrated system. And every accessory or component adds value, allowing you to be more productive.
Festool tools share similar characteristics with other brands. However, Festool engineers improvements on many of these tools to enhance safety, efficiency and durability. Festool also offers a variety of tools that are unique to the industry. For example, the Festool line of Domino joiners is unmatched by any other. They allow you to use loose tenon joinery – one of the simplest and most durable methods of joinery – making the Domino one of the most sought after tools in the Festool lineup.
With Festool, there is a commitment to quality, product longevity, professionalism and user comfort not found in other products. Plus each Festool machine is designed to work with the Festool HEPA dust extractors to remove wood chips and sawdust, helping to prevent inhalation of airborne dust particles that are now known to be harmful carcinogens.
Most customers – whether seasoned Festoolians or first-time users – come back to tell us how their new Festool tool has increased their productivity, making everything from set-up to cleanup a whole lot easier for them.
You can see the complete Festool line-up of power tools at FestoolUSA.com, or ask us about the line the next time you’re at Selectwood.
- Fun Festool Facts:
Founded in Germany in 1925 - All tools and accessories are still built in Germany
- Every product is designed to withstand heavy use without breaking down
- Festool holds over 300 patents and 80 awards (and counting!)
- Responsible for many firsts:
- first portable chain saw
- first orbital sander
- first portable circular saw with guide rail (a.k.a. track saw)
- first false joint saw
- first professional sander for profiles and edges
- first cordless drill with a brushless, electronically commutated motor
- The undisputed leader in dust control, so you can take control of your health
- Everything is backed by a 3-year, full factory warranty
- Risk-free, 30-day, money-back guarantee
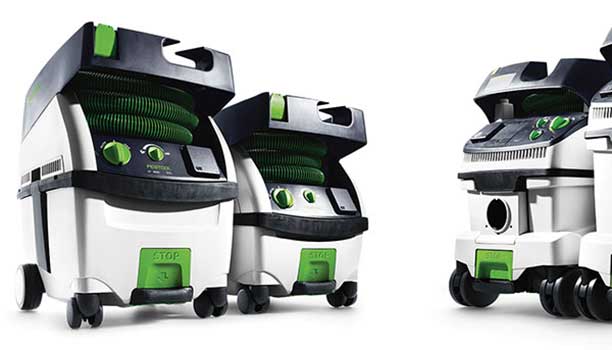
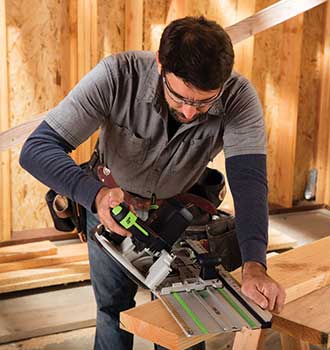
Ever since safety regulations started being codified for the construction industry, designers and manufacturers have worked diligently to meet those requirements in ways that are not only effective but aesthetically pleasing. Case in point: railings (“guard” in ICC codes). Whether we’re talking about balconies, decks or stairs, we can all agree that the safety of the people using these areas is paramount. And building codes reflect that: the top and bottom rails must be at certain heights from the floor/surface; the space between the infill elements cannot exceed 4″, etc… most builders know these codes by heart.
Read the Full Article
For decades, railings adhered to these regulations by using relatively thick balusters that created, in essence, short walls that allowed air to pass through and people to glimpse – in thin slices – what was on the other side. But when a house has a spectacular view to a panoramic vista, or an upper hallway that looks down into a magnificent great room, a baluster is literally a stick in the eye.
Enter cable railing systems. Cable railings are safety rails that use thin (typically 1/8″– 1/4″), horizontal or vertical cables for infill in place of those thick balusters. This allows a nearly unobstructed view while providing the same level of safety as traditional railings. Plus, cable railings have the added benefit of imparting a modern aesthetic to almost any design.
Cable railing systems, which originated on the West Coast, have been around for decades. In recent years, the use of cable railing systems in the northeast has grown dramatically and shows no signs of being a fad. (You know something is popular when realtors start including it in property descriptions!) But before you start installing cable rail systems on every staircase and deck, there are a few key points to consider:
Cables and Tensioning
There are many different types of cable: type 316 stainless steel is best for coastal areas. The old UBC (Uniform Building Code) and newer ICC (IBC and IRC) codes state that a 4″ sphere shall not pass through any portion of a barrier on a guardrail. As a result, cables that are spaced 3″ apart must be tensioned to 200-400 lbs. to they don’t deflect to 4″ between them.
Post Construction and Spacing.
The end posts to which the tensioning hardware attaches must be constructed so that they will not perceptibly deflect under the high tensioning load. While this is not difficult, it does require stronger material and more time and attention than a traditional frame. The intermediate posts provide support for the top rail and have a vertical row of holes to support the cable as it passes through between end posts. In our experience, a system is much stronger and lasts longer when posts are no more than 3 ft. on center.
Top Rails
The top rail must be strong enough to withstand the compression caused by the tension on the cables. Common top rail materials include metal and stronger species of wood. Composite lumber can be used with a support rail.
Cable Infill vs. Glass Infill
Some people – owners, architects and builders among them – prefer the look of tempered glass as infill. This can be extremely effective in the right climate/environment, but less so in the northeast. Cable railings allow easier snow removal and do not require periodic cleaning like glass, especially near the shore where salt spray is problematic. Also, cable railings are much more bird-friendly than glass, as birds can see the cables and avoid injury.
Cost
The initial cost plus the more involved installation put cable railing costs at about 30-40% higher than traditional, baluster-based railing systems. That said, the cost of maintenance is much lower – cable does not need to be painted or stained and can be cleaned by wiping with a damp cloth. And of course, how much are people willing to pay to ensure they don’t lose that million-dollar view?
Selectwood Recommends Feeney CableRail® & DesignRail®
California-based Feeney first started making cable railing systems in 1988. They’ve been improving and refining them ever since. We started offering Feeney products eight years ago and have had nothing but positive feedback from architects, contractors and homeowners alike. CableRail is designed to be used with your own wood or metal frame, while DesignRail is a complete aluminum railing system in your choice of 6 different caps and 8 standard colors… plus more than 200 custom colors! For more details, call Selectwood at 800.922.5655 and ask for Sales.
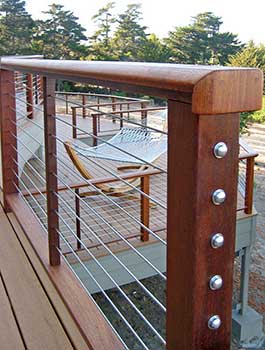
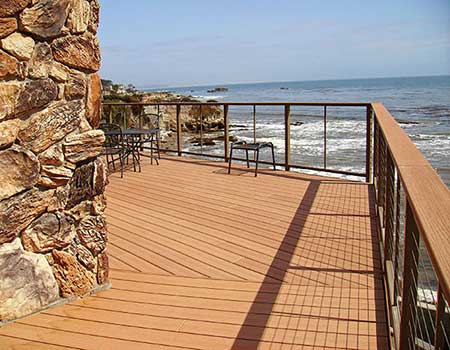
Several years ago we wrote about the relatively new successes Cellular PVC was experiencing in exterior trim applications. We thought it was time to take another look at Cellular PVC and examine its recent evolution in the building industry. But first a brief explanation what Cellular PVC is.
Read the Full Article
A New Front Deck Becomes A Neighborhood Gathering Spot
Dave and Cheryl Hill live in an incredibly friendly neighborhood in Sanford, ME. “People are always walking by,” says Dave. “And if you’re out in front of the house, folks will invariably stop and chat – sometimes for quite a while.” And that suits Dave and Cheryl just fine.
So when Cheryl wanted to add a deck where she and Dave could enjoy more time in the sun, she thought they should embrace that friendliness and build the deck out front. “I don’t know what I want it to look like,” said Cheryl, “but I’ll know it when I see it.” So Dave spent some time in front of the house using stakes, string and buckets to define the deck’s size, shape, height, how the front steps might integrate, etc. Cheryl interjected that she’d love to have benches and planters to enhance the curb appeal, so those were incorporated into the plans.
Once Cheryl had her deck fully envisioned, she waited for Dave (whom she fondly refers to as “The Procrastinator”) to begin construction. After a few months, she realized the project would likely not be completed before winter, so they agreed to hire builder Jim Savage. Jim took Cheryl’s vision and brought it to life using Simpson joist hangers, Azek decking, Cortex hidden fastener system, Azek trim and DuraShell lattice for the skirt. Once Jim completed the deck, The Procrastinator took over and built some beautiful Azek benches and Azek planters. He then ordered a couple of custom-colored Seaside Casual Adirondack Dining Chairs from our sister company, Great Bay Spa & Sauna.
How’s the new front deck working out? Well, over a sunny weekend this past spring, Dave spent so much time chatting with neighbors who were “just passing by,” he got sunburned on one side of his face. And Cheryl couldn’t be happier. (Not about the sunburn – about the deck!) Actually, Dave’s pretty happy about it, too… only now he keeps some sunscreen next to his chair.
A Facelift Gives The Dyer Home A Fresh, Updated Look
The windows in Harold and Valerie Dyer’s home in Somersworth, NH, had last been replaced in 1972. So the Dyers ordered beautiful new Marvin windows to replace the vintage vinyls, and hired builder Jim Savage to install them. (Savage again… are you seeing a pattern here?)
Harold offered to help Jim by doing most of the deconstruction himself. As he was pulling back the siding next to the windows, Harold thought maybe they should replace the old siding as well. So he and Valerie ordered pre-colored American Original Cape Cod siding. It looks like cedar shakes but is made from polypropylene, which lasts longer and shrinks/expands less than vinyl. They also ordered pre-primed Boral TruExterior Trim, which they had painted a dark green for contrast.
As he was removing the rest of the siding, Harold remembered that he had never been happy with the ventilation in the roof, so he decided to expand his demolition to include the old gutters, soffits and fascia. And now with the whole house stripped, it just made sense to wrap it in Blueskin VP100 before putting anything back on. So they did.
As Jim Savage was finishing up with the windows and siding, it became apparent to the Dyers that some of the old doors on the house just weren’t up to snuff, so they replaced a glass slider with a new Marvin slider, a wooden door to the garage with a color-matched ThermaTru door, and the old bulkhead with a Bilco steel door. They also replaced the garage doors for good measure.
“The outside is now done,” says Harold. “Course, we haven’t started doing the interior trim yet. Maybe I’ll save that for another article.” (Wow… who knew procrastination was contagious? 😉
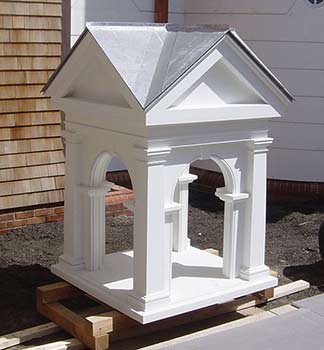
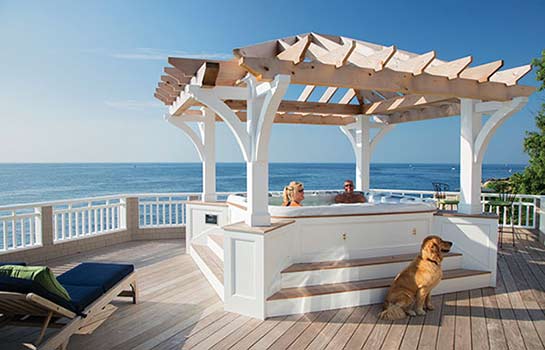
New Hampshire has a long-standing tradition of adhering to libertarian ideals. Most Granite Staters prefer less government and fewer rules to a larger state bureaucracy. We also enjoy “personal” liberties such as riding a motorcycle without a helmet, operating a car without wearing a seat belt, and carrying your favorite hand gun in the State House.
Read the Full Article
When the topic of licensing or registering building contractors comes up, many automatically view it as more government meddling in private business. One needs to study licensing before coming to quick conclusions. Contractor licensing can offer protection to consumers from under-skilled or dishonest contractors. Licensing can also protect good contractors from being underbid by bad contractors. However in our opinion, a poorly designed system that only results in more rules and restrictions, accompanied by needless government fees, would not be worth implementing.
Here’s the position of the New Hampshire Home Builder’s Association: “The NHHBA supports the licensing of builders and/or home improvement contractors where the required license or certificate is part of a program designed to promote professional standards, continuing education and fair business practices. The NHHBA continues to oppose legislation that falls short of these goals or that would unjustly or disproportionately impact the industry in pursuit of these goals.”
Currently about half the states in the U.S. require contractor licensing or registration. Some states appear to be merely collecting fees for contracting privileges (this is the type of licensing the NHHBA rejects), whereas other states operate effective systems with well-defined education requirements. Of the six New England states, Maine, New Hampshire and Vermont do not license homebuilders; the other three do. Rhode Island does require proof of insurance and tax documents, but no New England state requires a comprehensive educational program to build or remodel a customer’s home.
Should Builder Education Be Mandatory?
With the adoption of the State Building Code in 2010, New Hampshire took a step forward toward standardizing building practices. The N.H. code is based on the 2009 International Residential Code (IRC) and the 2009 International Building Code (IBC) and applies to both residential and non-residential structures. In addition to new construction, the code covers “alterations, renovations, repair, removal or demolition of all existing buildings and structures.”
The acceptance of the code was a positive first step in the adoption of safe, modern building practices in N.H. It provides builders and building officials standards by which they can judge whether a construction practice is appropriate. Still, there is no way to know if a builder is well versed on the code. And with building techniques and codes becoming more sophisticated, ongoing education becomes essential. There are some builders who are motivated to educate themselves, but there are others who will never find the time to do so. Mandatory education and testing is critical to insure all builders use sound building practices. Quite often after hearing case studies of job site deaths or serious injuries, builders are far more likely to use safe building practices.
To be effective, educational requirements must be reasonable and ongoing. In N.H., we require licensing and education for plumbers and electricians, yet the builder, who should be capable of evaluating their work, has no educational requirements. The N.H. code stipulates that the “contractor of a building shall be responsible for meeting the minimum requirements of the state building code.” Most often a town or city building inspector will review the work of a builder, yet it shouldn’t be the inspectors’ job to educate builders.
Can Licensing Help Reduce Contractor Fraud?
Even in “honest” New Hampshire, stories of faulty contracting jobs abound. Often it’s hard to determine if a contractor is unscrupulous or is just incapable of performing the contracted work. Often disputes over home improvement or building work end up in small claims court to sort out what actually happened. And even if a contractor defaults or is found to be at fault, there is no guarantee a consumer will ever recover their money.
Wouldn’t it be good for the consumer to know that a potential contractor has fulfilled standard licensing requirements? An online state registry would make researching a contractor easy. This would give the good guys an advantage in securing work while not having to worry about being underbid by crooks. Registration or licensing would also benefit the consumer by ensuring the contractor is properly insured. If a general contractor has employees, licensing would prove he has appropriate payroll withholding systems and insurance in place to protect his employees.
How This Could Work.
Building inspectors want safe, honest, educated, professional contractors. As stated previously, the NHHBA will not endorse a statewide licensing plan unless a comprehensive educational requirement is included. With the rich educational resources of the New Hampshire Home Builders Association, which is closely affiliated with the National Home Builders Association, we already have a great start. It would make little sense for the State of N.H. to get involved with educational accreditation. Some people will argue that licensing contractors will make construction more expensive. We couldn’t find any facts to support that claim. States that have successful licensing programs should be studied for what might work in N.H.. For instance, in Florida they allow a handyman to perform jobs up to $1,500.00 without being licensed.
We Propose a Standardized N.H. Construction Contract.
When considering whether to license builders in N.H., we should also consider a simple, standardized, fill-in-the-blanks N.H. Construction Contract. Many disputes between builders and consumers happen when the ground rules are not well defined. A standardized contract could be a tool for recording information on the builder, including license validation and insurance information. Additionally, the contract could disclose if the builder will be using his employees or independent contractors to perform work. If the contract has a fixed price, it could define how change orders would be billed. If the work is to be performed on a time-and-materials basis, it would outline the labor rates and the formula for billing materials. A standardized contract would protect both consumers and honest builders.
Licensing – in addition to protecting consumers, promoting safer building practices and establishing a level playing field for competitive bidding – would have one additional benefit: A contractor could take pride and satisfaction in achieving the educational goals and have the right to refer to himself as a licensed N.H. Contractor. Anyone can print business cards; have lettering installed on a pick-up truck, and poof… instant homebuilder! The ability to pass comprehensive testing and meet insurance requirements raises the bar and helps create professional credibility. Being able to call yourself a Licensed Contractor implies that you have earned that title. Let’s work to give homebuilders’ and their profession the respect they deserve.
Licensed Contractor implies that you have earned that title. Let’s work to give homebuilders’ and their profession the respect they deserve.
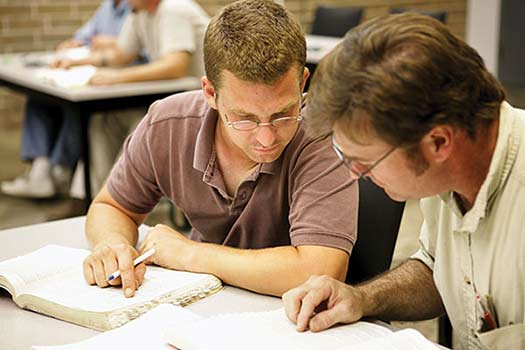
Contact
Map
Email Signup
LOCATION
Eldredge-Selectwood
275 Constitution Avenue
Portsmouth, NH 03801
Call: 800.922.5655
Local Phone: 603.436.9663
Fax: 603.436.1331
E-mail: dkeith@eldredgelumber.com
Store Hours:
Mon. – Fri.: 7:30 am – 5:00 pm
Saturday: 8:00 am – 1:00 pm